If you’re a home services contractor, understanding the intricacies of HVAC permits is a business necessity to keep your projects on schedule and protect cash flow. It’s also vital for staying compliant, avoiding costly rework, and maintaining your reputation as a reliable contractor.
In this guide, we cover everything you need to know about HVAC permits — from when they’re necessary to how much they cost and everything in between.
Pull HVAC permits faster with PermitFlow. Learn how.
When do you need an HVAC permit?
Most residential and commercial HVAC projects require permits — especially if modifications or additions affect major building systems or occupant safety.
As a rule of thumb, any work that changes equipment capacity, alters gas or electrical connections, or penetrates the building envelope requires an HVAC permit.
Some examples of these include:
- Installing a new furnace, central air conditioning, or a heat pump
- Replacing an older HVAC system with newer, energy-efficient models
- Extending or relocating ductwork
- Adding new zones to an existing network
- Connecting gas lines to heating appliances
Ultimately, every jurisdiction has its own requirements, so you'll need to check with the local AHJ.
That said, inspectors everywhere watch for three red flags:
- Safety risk: New fuel lines, flue vents, refrigerant piping, or high-voltage circuits.
- Energy impact: Equipment SEER2/HSPF ratings, duct leakage, or envelope penetrations that fall under the IECC or Title 24.
- Structural load: Curb adapters for rooftop units, pad upgrades for condensers, or attic platforms for air handlers.
If you’re looking for what your unique municipality requires in regards to HVAC permits, check out PermitFlow’s Municipal Guides.
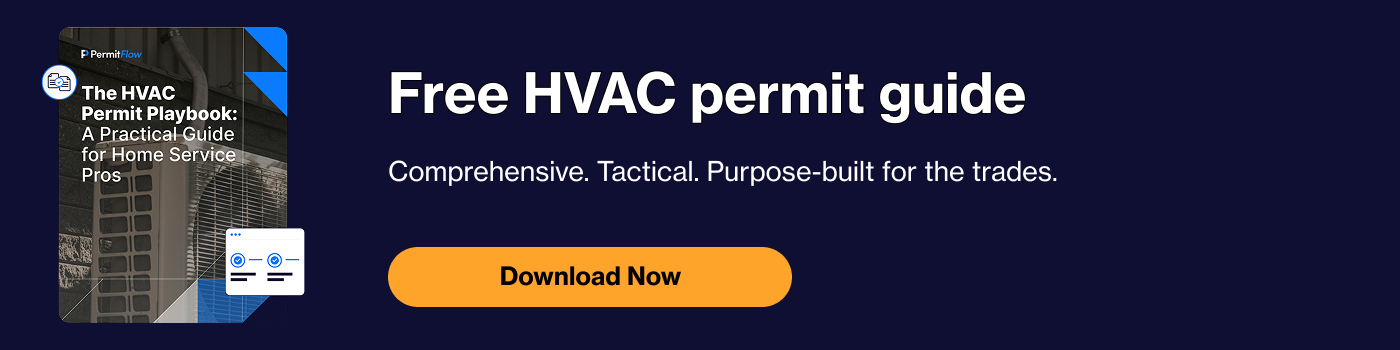
What doesn’t require an HVAC permit?
Not every HVAC project requires a permit. Most jurisdictions carve out an “ordinary maintenance” category so contractors can keep systems running without submitting an HVAC permit application every time. The common thread is that you don’t alter capacity, fuel type, or branch circuits.
Here’s a more complete list of work that’s typically exempt — plus a few caveats that keep you out of trouble:
- Filter replacements and routine coil cleaning
- Caveat: Just keep in mind that swapping in a larger media cabinet that requires duct modification could bump it into permit territory.
- Thermostat swap (battery-powered or same-voltage smart stat)
- Caveat: Running new control cable inside walls or adding a 24-V transformer counts as an electrical alteration that requires a permit.
- Duct and register cleaning
- Caveat: Installing new duct sections or adding take-offs to improve airflow is a structural change that requires a permit.
- Minor electrical repairs on the condenser whip or furnace disconnect (same conductor size/ampacity)
- Caveat: Upsizing the breaker, adding a new disconnect, or extending the circuit needs both electrical and HVAC permits.
- Refrigerant top-off (no component replacement)
- Caveat: Replacing the evaporator coil or line set triggers a rough-in inspection for pressure test and insulation.
- Combustion tune-up or safety-control calibration
- Caveat: Any new gas valve, regulator, or piping extension requires pressure test sign-off.
Do you need a permit to replace HVAC equipment?
You almost always need a permit to replace HVAC equipment.
Most U.S. building departments treat any installation or modification of heating or cooling equipment — including a 1‑for‑1 swap — as “mechanical work,” which requires a permit and at least one inspection.
This is because newer equipment must meet current energy and safety codes, and the installation must be inspected for:
- Proper airflow and ventilation
- Secure electrical and gas connections
- Code-compliant clearances and anchoring
- Environmental compliance for refrigerant handling
Depending on the jurisdiction you’re located in, there may be exceptions to these rules. Some jurisdictions might allow simple rooftop unit swaps or packaged systems under a certain BTU threshold to proceed without a permit. Still, it’s better to double-check than to assume.
Don’t waste time researching permitting requirements in your jurisdiction — let PermitFlow do it for you. Learn more.
HVAC permit costs
HVAC permit fees vary by location, project type, and how your local building department calculates costs.
While there’s no universal rate, most U.S. jurisdictions follow one of these pricing models:
- Flat fees: Common for residential jobs, typically $75–$300
- Valuation-based: Charged per $1,000 of job cost, usually $8–$15, with minimums around $100–$150
- Fixture-based: Based on number/type of HVAC units
Several elements influence HVAC permit fees:
- Project type: Permits for new construction and full system installs typically cost more than for basic equipment swaps.
- Property type: Permits for commercial and multifamily projects generally carry higher fees and may require plan check fees.
- Local regulations: AHJs in cities with strict energy codes (e.g. California Title 24) or extreme climate zones may charge more for HVAC permits due to additional review steps.
The HVAC permit application process
Even experienced installers can lose days (and profit) when a permit submission is incomplete. Use the checklist below to move from bid to approved HVAC permit — and onto the job site — without back-and-forth delays.
While every jurisdiction has its own requirements and process, typically you’ll see these 5 general steps:
1. Determine the need
Verify that the scope meets the threshold for a permit (new equipment, capacity change, duct relocation, gas-line tie-ins, etc.).
Pro tip for contractors:
Call the AHJ before you quote — some jurisdictions now require a permit for HVAC replacement even for 1-for-1 swaps if the SEER rating changes.
2. Gather technical documentation
Permit applications require extensive documentation that outlines all pertinent details about the project.
You’ll probably need to prepare:
- Equipment data sheets (model, BTU/tonnage, efficiency)
- ACCA Manual J/S load calculations or Title 24 compliance forms (where applicable)
- Duct layout/Manual D or manufacturer’s engineered design
- Electrical one-line diagram and breaker sizing
- Gas piping schematic & CSST bonding details
Pro tip for contractors:
Upload PDFs in the naming format the plan reviewer prefers (e.g., “LoadCalc_123 Main.pdf”). It prevents lost attachments and speeds up review.
3. Submit the application
The local building department might have an online portal where you submit your application. Otherwise, you’ll probably need to mail it in or bring it in person to the department’s office.
In addition to technical documentation, you’ll usually have to provide administrative details like contractor license number, project valuation, and contact details, alongside required permit fees (if required before approval).
Make sure your submissions are as detailed and accurate as possible to ensure a speedy review. Incomplete plans or plans with minor errors are the main reason why permit applications get delayed.
Pro tip for contractors:
Enter the same project valuation on every form (permit, utility rebates, homeowner invoice) to avoid red flags that trigger audits.
4. Monitor plan review
The amount of time it takes for the department to review your application depends on the scope of your project and how busy they are. For a simple, over-the-counter equipment swap, you might be approved in a day, whereas it could take a week or more if the project involves extensive mechanical plans.
Pro tip for contractors:
Set calendar reminders at 3-day intervals. If the status hasn’t moved, a polite nudge with the permit number could bump it towards the top of the queue.
5. Pull the permit & post on-site
Print or download a copy of the permit and any inspection cards, and make sure they’re clearly visible at the job site.
Pro tip for contractors:
Laminate the permit and inspection card and zip-tie them to the air handler – inspectors find it fast, and you look buttoned-up.
Related reading: Navigating Complex Permits: A Guide to Specialized Construction Permits
HVAC permit inspections
Receiving your permit approval is just a step to a larger process — passing your inspections is ultimately where your hard work is validated. HVAC inspections typically happen in two different stages: the rough-in inspection and the final inspection.
The rough-in inspection
This type of inspection is performed before the walls are sealed so inspectors can see the work being done.
This inspection often covers:
- Ductwork layout and sealing
- Refrigerant line placement
- Gas line installation and venting
- Electrical rough-ins for HVAC controls
Final inspection
This inspection happens once the system is fully installed and operational.
The inspector will check:
- System startup and shutdown functions
- Thermostat operation
- Combustion air supply and exhaust routing
- Proper labeling and documentation
- Secure mounting and weatherproofing (for outdoor units)
Inspectors are looking for compliance with mechanical, electrical, and energy codes. Be prepared with documentation and load calculations, and provide access to all necessary components of the system.
HVAC permit inspection after installation
If your system passes inspection, the building department will issue a final sign-off and close out the permit. This confirmation is often required for final payment, insurance coverage, or resale documentation.
If the installation fails inspection, you’ll receive a list of deficiencies that must be corrected before scheduling a reinspection. Reinspection fees may apply, so it’s in your best interest to do the work correctly the first time around. As a contractor, a successful completed inspection record protects you from liability and proves your commitment to providing safe, compliant, and reliable work for your customers.
Consequences of doing HVAC work without a permit
Skipping the permit process can seem tempting when deadlines are tight — but it’s just not worth the risk.
Working without a required HVAC permit can result in:
- Stop-work orders and fines
- Forced removal of unpermitted equipment
- Liability exposure for safety hazards or damages
- Delays during appraisals or home sales
- Loss of client trust and reputation
Unpermitted work also voids most manufacturers’ warranties and can lead to denied insurance claims if something goes wrong.
Pull HVAC permits efficiently with PermitFlow
For home services contractors, pulling the proper HVAC permit is more than a regulatory requirement — it’s an important professional responsibility. But permits shouldn’t be the bottleneck that keeps your crew in office and off a job site.
PermitFlow can do the heavy lifting for you. Our team of experts will pinpoint exact permitting requirements in your jurisdiction and let you know exactly what documentation is required.
Upload your plans and PermitFlow will handle the rest: completing your application, submitting it to the appropriate department, and tracking approvals in real time. No phone-tag, no surprise resubmits.
Talk to our experts today to learn how PermitFlow can help you save time pulling HVAC permits.